Comprehending Welding WPS: Comprehensive Overview for Welders
Comprehending Welding WPS: Comprehensive Overview for Welders
Blog Article
Achieving Welding Excellence: Revealing the Tricks of WPS Application and Optimization
In the world of welding, attaining excellence is a pursuit that hinges on the precise application and optimization of Welding Procedure Requirements (WPS) These fundamental records offer as the foundation of welding procedures, determining the treatments and specifications needed for creating premium welds continually. Nonetheless, the keys to opening the complete capacity of WPS lie not just in recognizing its relevance but likewise in understanding the intricacies of its application and optimization. By diving right into the crucial elements, approaches, obstacles, and best techniques connected with WPS, a world of welding excellence waits for those that are prepared to explore its midsts.
Value of WPS in Welding
The Value of Welding Treatment Specs (WPS) in the welding market can not be overemphasized, serving as the foundation for making sure consistency, high quality, and security in welding operations. A WPS provides thorough guidelines on exactly how welding is to be carried out, consisting of important variables such as products, welding processes, joint style, filler metals, interpass and preheat temperature levels, welding currents, voltages, traveling speeds, and extra. By adhering to a distinct WPS, welders can keep uniformity in their work, bring about regular weld top quality across various tasks.
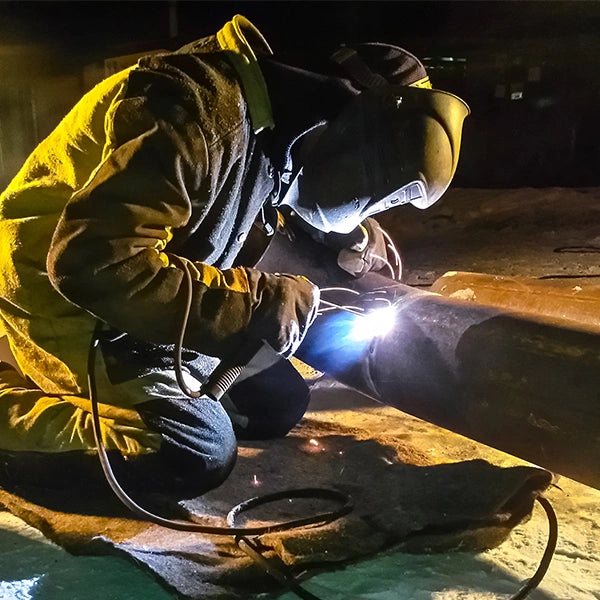
Key Elements of WPS
Discussing the essential elements of a welding procedure spec (WPS) is important for comprehending its function in welding procedures. A detailed WPS includes several crucial elements that guide welders in attaining high quality and uniformity in their job. One critical aspect of a WPS is the welding process specification, which describes the details welding procedures to be utilized, such as gas tungsten arc welding (GTAW) or protected steel arc welding (SMAW) Additionally, the WPS consists of details on the welding materials, such as the type and specifications of the base steel and filler metal to be utilized. The WPS also defines important variables like welding parameters, interpass and preheat temperature needs, and post-weld warm therapy procedures. Furthermore, it includes details on joint style, fit-up, and any type of special strategies or precautions required for the welding procedure. By integrating these vital components right into the WPS, welding procedures can be standard, guaranteeing high quality, performance, and security in welding procedures.
Methods for WPS Optimization
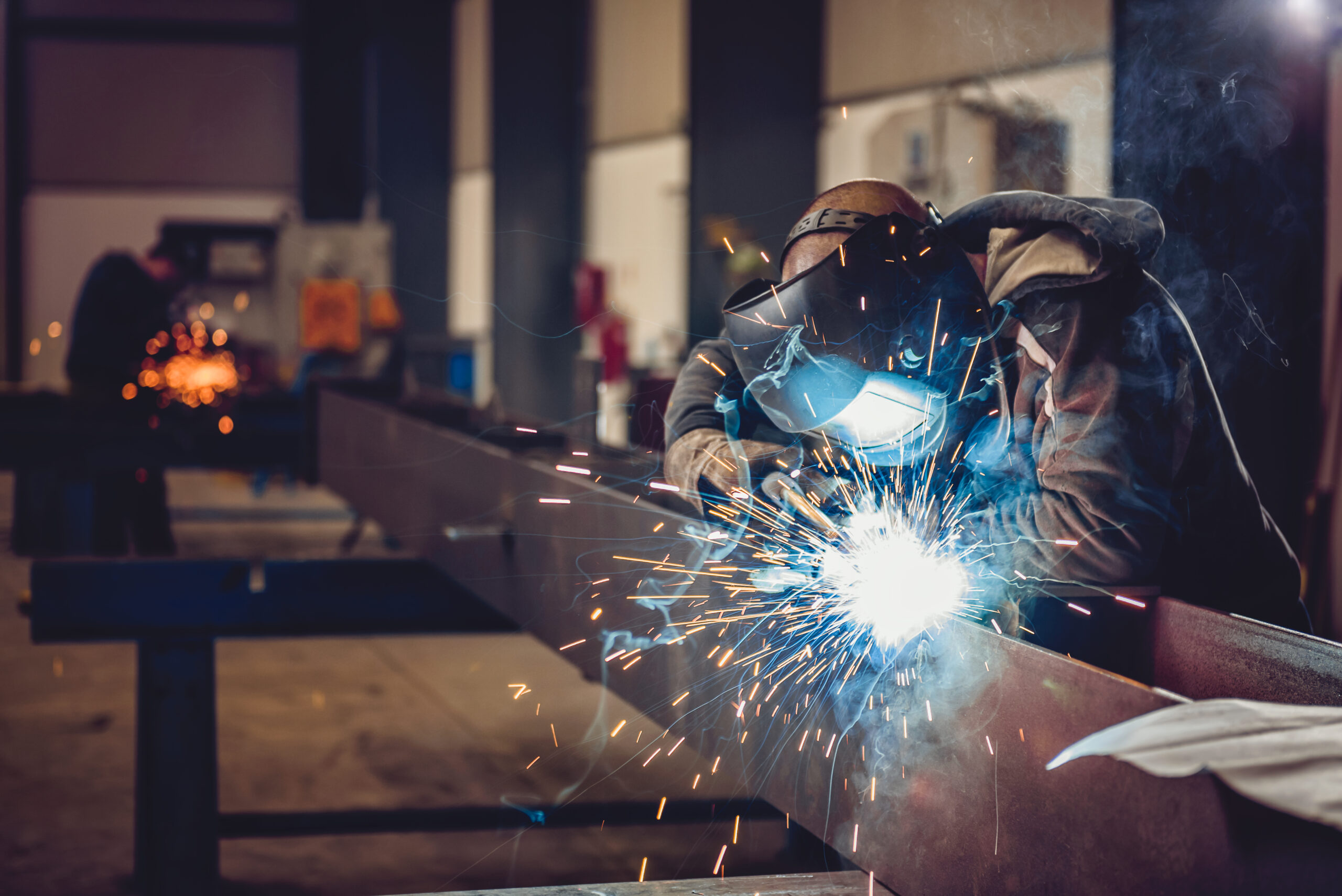
Second of all, training and credentials of welding personnel according to the certain needs of the WPS is vital. Supplying thorough training programs and ensuring that welders are certified to execute treatments detailed in the WPS can result in better welds and minimized rework.
Additionally, leveraging modern technology such as welding software application and tracking systems you could try this out can assist in enhancing WPS. These devices can assist in tracking variables, making certain criteria are within defined limits, and providing real-time feedback to welders, allowing them to make instant modifications for boosted weld quality.
Typical Difficulties and Solutions
Encountering challenges in carrying out the approaches for WPS optimization can hinder welding procedures' performance and quality. One usual challenge is insufficient training or understanding of the welding treatment requirements (WPS) amongst the welding team.
An additional challenge is the lack of appropriate paperwork and record-keeping, which is necessary for WPS optimization. Without clear documents of welding specifications, products used, and examination results, it ends up being difficult to recognize locations for enhancement and make sure consistency in welding processes. Carrying out a robust documents system, such as digital welding administration software program, can help simplify record-keeping and assist in information evaluation for continuous improvement.
Additionally, inconsistent welding tools calibration and upkeep can position a considerable difficulty to WPS optimization. Normal devices checks, calibration, and maintenance schedules should be complied with strictly to make sure that welding parameters are properly controlled and preserved within the specified tolerances (welding WPS). By resolving these typical challenges with proactive solutions, welding operations can enhance effectiveness, quality, and total welding quality
Best Practices for WPS Application
To ensure effective WPS execution in welding operations, adherence to market standards and careful interest to information are critical. When launching WPS execution, it is critical to start by extensively comprehending the details welding requirements of the job. This requires a comprehensive evaluation of the welding treatment specifications, products to be bonded, and the environmental conditions in which the welding will happen.
As soon as the requirements are clear, the next step is to pick the appropriate welding procedure that lines up with these specs. This entails consulting the appropriate codes and criteria, such as those provided by the American Welding Society (AWS) or the International Organization for Standardization (ISO), to make sure conformity and top read the full info here quality.
Furthermore, documenting the whole WPS execution process is important for traceability and quality assurance. In-depth documents must be maintained regarding welding specifications, material preparation, preheat and interpass temperatures, welding consumables utilized, and any discrepancies from the initial procedure. Regular audits and reviews of the WPS can help recognize locations for renovation and make sure continuous optimization of the welding process.
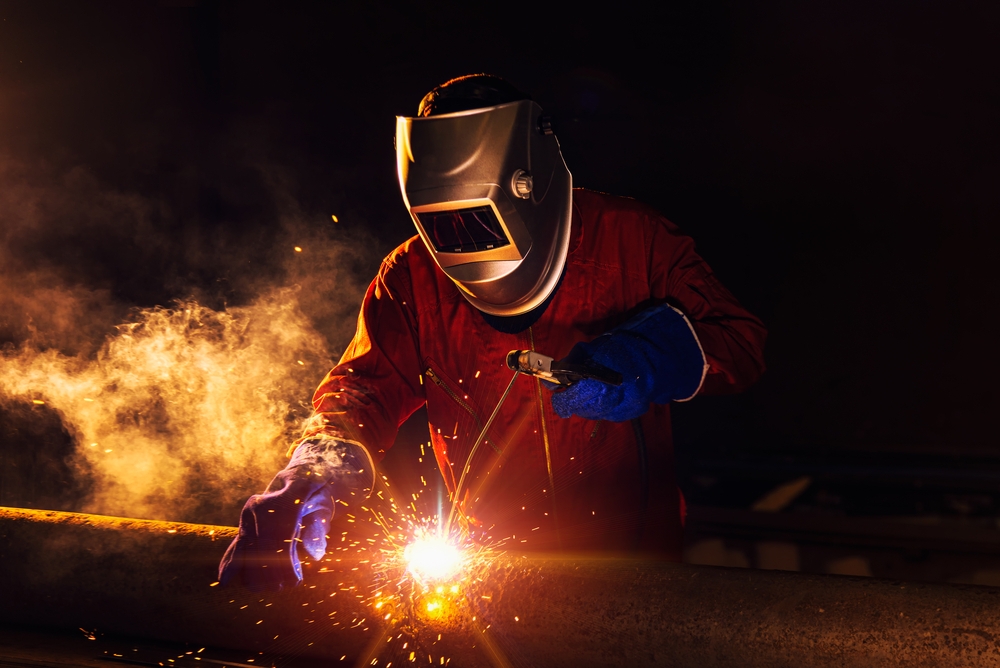

Conclusion
To conclude, the implementation and optimization of Welding Procedure Requirements (WPS) is important for attaining welding quality. By understanding the crucial components of WPS, executing efficient approaches for optimization, attending to common challenges, and complying with ideal techniques, welders can guarantee top quality welds and risk-free working problems. It is click here for info crucial for specialists in the welding industry to prioritize the correct implementation of WPS to boost overall welding efficiency and achieve desired outcomes.
The Significance of Welding Procedure Specs (WPS) in the welding market can not be overemphasized, offering as the backbone for guaranteeing consistency, quality, and safety in welding operations. A WPS provides detailed directions on exactly how welding is to be lugged out, consisting of important variables such as materials, welding processes, joint style, filler steels, preheat and interpass temperatures, welding currents, voltages, travel speeds, and much more. One important element of a WPS is the welding process specification, which describes the specific welding processes to be made use of, such as gas tungsten arc welding (GTAW) or protected metal arc welding (SMAW) By integrating these essential elements right into the WPS, welding treatments can be standardized, ensuring top quality, performance, and safety and security in welding procedures.
It is necessary for experts in the welding industry to focus on the correct application of WPS to enhance total welding efficiency and accomplish desired end results.
Report this page